Die Design Fundamentals for Transfer and Progressive Dies. Progressive die design As already noted the overall production requirements are the main factors in considering the size of a die and the number of finished products per stroke of the press.
Ad We have a combined 60 years in the tooling industry and over 15 years in contract service.
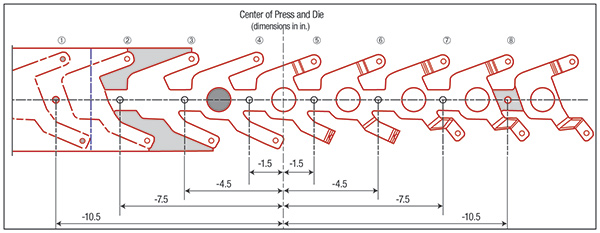
. Tool Designs for the Metal Stamping Industry. An expert system for design of progressive die ESPDIE has been developed for die designers working in sheet metal industries. The Anatomy of a Die Cut A normal metal stamping process creates a die cut is to drive a sharpened tool steel punch through the sheet or strip material into a die cavity where the slug or scrap is ejected.
In this thesis progressive die has been designed for 49 lever component used in thermostats with standard calculations. Mexico LatinAmerica VARInfo. Also known as webs strips ties and attachments the types of carriers and their shapes vary.
Progressive dies washers Design forces for punching and blanking 1DESIGN OF PROGRESSIVE DIE A. The modeling of progressive die is done using ProEngineer package. 51 Die Clearance Calculation Clearance per side C t η max10 Where C constant C 0005 very accurate component C 001 normal component t sheet thickness 15 mm Clearance per side 001 15 36010 Clearance per side 009 mm per side 52 Plate thickness Calculation Thickness of Die Plate td 3Fs.
Any manual for FEM forming simulation analysis for deep drawing in ANSYS. 19 May 2014 0951 AM. Can anyone give me any reference for deep draw punches diameter calculations.
The modelling of progressive die is done using ProEngineer package. Hi everyone I need some support for Deep Drawing Process. REFERNCES 1 Dieter G.
NX Progressive Die Design is a comprehensive solution for quality die design supporting associativity with the part design at every stage of die development and including a variety of functions specific to automotive pro-. This course provides the thought process work flow for how a die design is established and the items to consider for building dies internally or sourcing to an outside supplier. Progressive die is used for high rate of production.
The component can be produced with accurate dimensions. Blanking is often a series of cutouts used to trim the flat coil material and define the edges of the final product. It is the design of die structure and sequencing of complete stamping process.
Process automation NX Progressive Die Design streamlines the die development process from design through to tool validation. One of the most time-consuming and difficult-to-predict aspects of die build and tryout for progressive dies is the development and validation of the blanking cuts. Learn the inputs concepts and requirements for design of dies for Transfer Progressive Die Line-ups.
Progressive die developed blank and trim line development. It allows quick modeling of the true solid 3D strip in a very. No die design software is complete unless it has a thorough Intelligent.
The strip layout module can be used for both progressive dies and transfer dies. In the process of designing a die structure the engineers establish how many principal and subsidiary elements are required in the process. Automatic K-Factor calculation for each individual bend Customizable and flexible bend.
Let us consider a requirement for 1000000 washers per week to be produced in a press capable of delivering 150 strokes per minute. Production rule based expert system is utilized for constructing. University of Northern Iowa Midwests Top Public University.
On the other hand the planning of stamping process as the name suggests is creating a project plan of the overall progressive. Progressive Die Design. Forces are calculated when blanking and bending operations are done.
The component can be produced with accurate dimensions. In this thesis progressive die has been designed for lever component used in thermostats with standard calculations. Forces are calculated when blanking and bending operations are done.
With all material running through progressive stamping dies we find the carrierthe material that connects holds and transports the stampings from station to station as they move sequentially through the die. The die bore Punch diameter 2 Die clearance 26 Calculation Of Force force The cutting force applied in the punch to perform a punching operations such as piercing and blanking in the stock material can be calculated by the actual shear. Cutting clearances between the punch and die are closely defined and specified in the die design stage based on the requirement of the part.
Regarding progressive die design of progressive die is simple. This design procedure can also be extended for manufacturing washers for M-series bolts by modifying the punch and die plate dimensions. Stripping force required kLTÏ„ Kstripping constant 00207for low carbon steels above 15 mm thickness 00207Ï€1401808390 320618N 03206KN Total forceshearing force stripping force 1112103206 11150KN Capacity of press required for punching operation1115KN.
Advantage of progressive die is it perform two or more operations simultaneously by a single stroke.
Solved Answer The Following Questions 1 Design A Chegg Com
Metal Stamping And Die Design Blanking Machinemfg
Metal Stamping And Die Design Blanking Machinemfg
Progressive Dies And Tipping Moments Metalforming Magazine Article
Nx10 Progressive Die Design Steel Stamping Set Press Tool Design Video Tutorials Youtube
0 komentar
Posting Komentar